Iron Ore Mine
The iron ore mining area located at an altitude of 1,600 meters, characterized by extreme temperature variations ranging from -40°C to 50°C, and challenging conditions including dust, rain, and snow. The mining site faced significant operational and logistical challenges, prompting the client to seek our advanced tele+AI solutions to enhance safety, efficiency, and operator comfort.
Challenges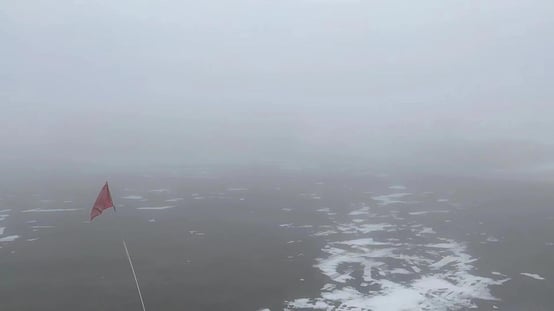
Prior to implementing our solutions, the client encountered several critical issues:
- Extreme Environment: The mining site’s severe weather conditions, including high winds, large temperature fluctuations, and harsh dust and snow, created a demanding work environment for operators.
- Operational Efficiency: The harsh conditions and the need for frequent equipment inspections and shift handovers led to considerable downtime and inefficiency. Each round trip for shift handovers cost about one hour, significantly reducing effective working time.
- Safety and Comfort: The challenging environment posed risks to operator safety and well-being, necessitating long commuting times and exposure to extreme weather.
Solution
Our tele+AI solutions were implemented in two phases to address these challenges.
First Purchase in 2021:
- Equipment: TZ WK-10C (electric shovel) and XCMG XE3000 (hydraulic shovel).
- Network: 5G Private Network.
- AI Functions: Remote Flamemout/Shutdown, Auto-Loading, and Pedestrian Detection.
These features allowed operators to control machinery remotely, reducing physical strain and exposure to harsh conditions.
Second Purchase in 2023:
- Equipment: TZ WK-10B, WK-20, WK-4C (electric shovels), KY-310 (drilling rigs), SF31904C (mining trucks), PLK4500 (bulldozers).
- Network: 5G Private Network.
- AI Functions: Expanded to include the same advanced functions of remote control, auto-loading, and pedestrian detection, enhancing the efficiency and safety of a broader range of equipment.
Implementation
The implementation process was carefully managed to ensure seamless integration with existing operations:
- 2021 Retrofit: The initial retrofit involved installing remote intelligent control systems on the TZ WK-10C electric shovel and XCMG XE3000 hydraulic shovel. These systems provided real-time audio and vibration feedback, enabling operators to make informed decisions remotely.
- 2023 Expansion: Building on the success of the initial implementation, additional remote control systems were installed on six electric shovels and two soil discharge machines. Our team provided comprehensive training to operators, ensuring they could effectively utilize the new technology.
Results
The results of our tele+AI solutions were transformative:
- Enhanced Efficiency: Achieved an average of 6.5 minutes to complete loading of 7 buckets per truck during night operations, significantly improving operational productivity.
- Reduced Commuting Time: Operators’ daily commuting time was reduced by 3-4 hours, allowing more focus on productive tasks and less time spent in transit.
- Increased Operational Time: Each piece of equipment gained an additional hour of effective operation per day, resulting in substantial economic benefits for the mine.
- Improved Safety and Comfort: Operators experienced relief from the extreme working environment, enhancing their overall job satisfaction and reducing health risks associated with harsh conditions.
Overall, our tele+AI solutions have significantly improved the efficiency, safety, and working conditions at the iron ore mining site, demonstrating the transformative potential of advanced technology in challenging environments.
Why not
Choose the Best
Get a detailed consultation